Others also bought:
Similar items
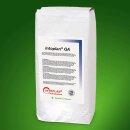
28,80 € - 64,80 € *
1,15 € per 1 kg
More variations available.
More variations available.